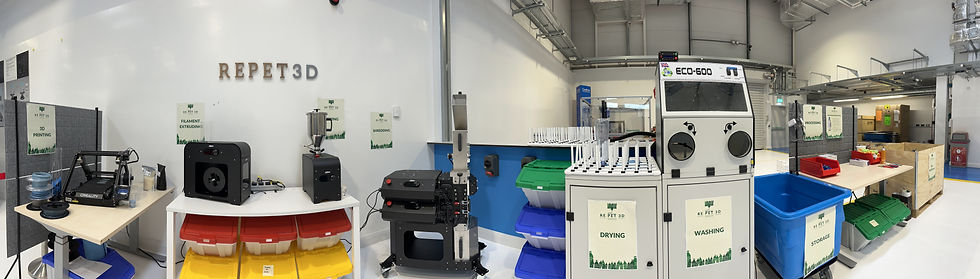
Re pet 3d
RePET3D is a project that recycles used plastic water bottles converting them into 3D printing filament. This project was completed as part of the UL50 Sustainability Challenge 2023. The team developed a material processing line, where we input old plastic water bottles, and they are washed, dried, shredded, and extruded into PET 3D printing filament.
​
The team consisted of Dr. Alice Shannon, EmmaJude Lyons, and Dr. Aidan O'Sullivan

All Videos

Raw material
The team worked with the UL Student Life, participating in Charity Week and Race Day to collect plastic water bottles from the UL student community as the raw materials for the project. We also used bottles that were collected in a bottle drive on campus in the past.

Drying
To dry the plastic bottles, we created a custom drying rack which circulated air through the bottles. In keeping with repoursing, we used an old bouncy castle blower to circulate the air and dry the bottles
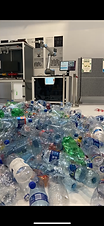
Processing
The plastic water bottles were sorted into categories, including brand, color, and size. In processing the cap and closure ring were removed, and set aside into a Polypropolene category for processing at a later time. Finally, the label and glue were removed.

Shredding
With our new 3Devo Shredder, we shredded the plastic water bottles to create PET granules, which we re-dry in case of any excess moisture retention.
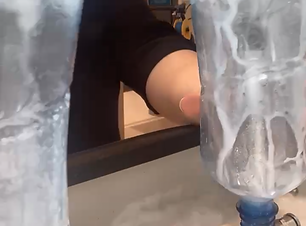
washing
As a sustainability project, we wanted to repurpose many items for the processing line. We repurposed a self-contained wash station for the post-processing of 3D-printed parts and modified it so it could wash the inside of the bottle.
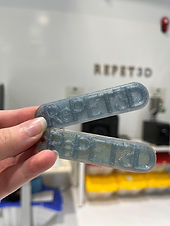
extruding
Post-drying, the granules are input into the 3Devo extruding machine, there are a range of temperatures set, and PET filament is extruded and ready for 3D printing.
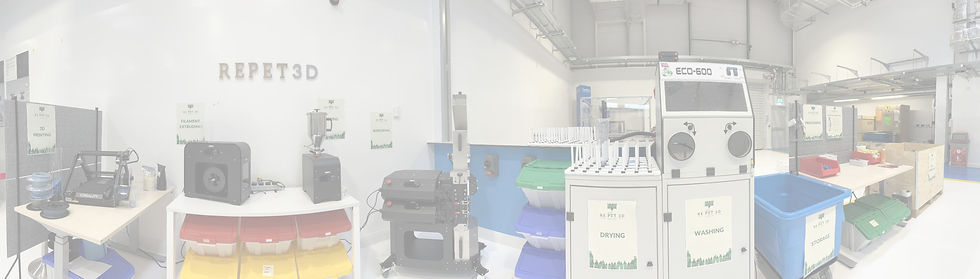